The project aims to capitalize on the successful fabrication of large scale crack-free yttrium-hydride through the design of an yttrium-hydride moderated micro-reactor. The micro-reactor will provide reliable, mobile, autonomous, safe operation for rapid deployment scenarios. Yttrium hydride is an optimal choice for heat pipe cooled, compact reactors. It has a high thermal stability which is required while using sodium filled heat pipes. It has a moderation ratio that is high in comparison to other hydride metals.
Team: Jillian Kasun, Brendan Lutz, Jeff Melo, Chase Olson, Max McKee
Project Advisor: Professor Danon
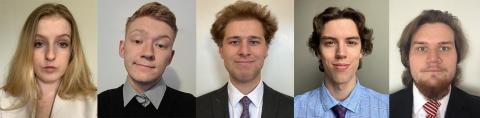
Members of the design group
Project Motivation
A niche demand for consistent, low-maintenance power to microgrids exists in locations such as remote islands, mining operations, military forward operating bases, and areas affected by natural disasters. A micro-reactor satisfies this demand, providing consistent power in a compact space and requiring little to no operator intervention or refueling. To compete with alternative power generation sources, a micro-reactor must be portable, have a quick set-up time, be able to load follow, and provide a consistent level of power for an extended period of time. The use of yttrium-hydride as a moderator is promising due to its high density of hydrogen atoms, enabling a more compact reactor design. This, combined with the high thermal stability of Yttrium hydride in comparison to other metal hydrides provides the impetus for this project’s design. Designing a yttrium-hydride moderated micro-reactor would allow for a compact enough form factor for a nuclear reactor to offer a competitive alternative to conventional power generation for microgrids.
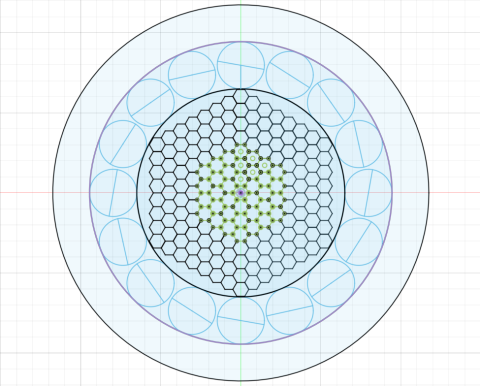
Figure 1- Schematic layout of the fuel elements.
Project Description
The project aims to capitalize on the successful fabrication of large scale crack-free yttrium-hydride through the design of an yttrium-hydride moderated micro-reactor. The micro-reactor will provide reliable, mobile, autonomous, safe operation for rapid deployment scenarios. Yttrium hydride is an optimal choice for heat pipe cooled, compact reactors. It has a high thermal stability which is required while using sodium filled heat pipes. It has a moderation ratio that is high in comparison to other hydride metals.
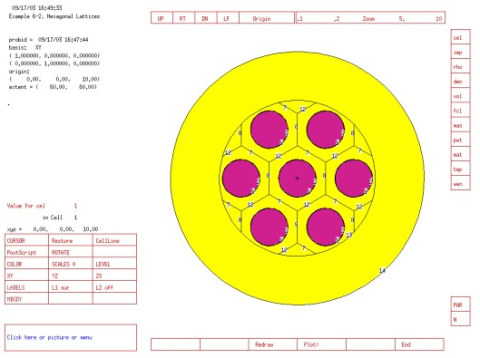
Figure 2 – MCNP Simulation of core elements.
Results and Accomplishments
The core design will implement a cylindrical core geometry with 11 m in height and 1.3 m in diameter, with space being allocated for both the shielding and the control drums. The fuel will be High Assay Low Enrichment Uranium Dioxide with 20% enrichment. There will be approximately 33.885 kg of U-235 fuel in 169.430 kg total fuel. The approximated pitch is 9.94 cm with approximately 150-200 individual fuel elements with space for control rods and heat transfer elements. The flux produced is in the order of 1012 neutrons/cm2.
The reactivity control subgroup has concluded three methods for neutron population control: control rods, control drums, and axial reflectors. The core will be calibrated with the 4 control drums at the beginning of the cycle to assure that the reactivity can be reduced to start. The control drum system will be used for neutron population control as well as increased core lifetime. The passive reactivity control will come from the negative temperature coefficient for reactivity. This will aid in reactivity control primarily in transient scenarios but will not provide any assistance in load following capabilities. The method for turning off the reactor will be 4 control rods that will be fully inserted into the core. An MCNP simulation has been started to simulate the core reactivity. Kcode will be used to do simple criticality calculations to assure the core can remain critical with the changing fuel burnup, the differing drum reflector and absorber composition, as well as the axial reflector. The control rods and control drums will use Boron-10 as the absorption material. The control drums and axial reflector will use Graphite as the reflector material.
The cooling subsystem will consist of heat pipes which contain molten salt as a working fluid. The molten salt will provide intrinsic safety precautions, as well as ease of transportation. Heat pipes provide a passive cooling solution that promotes autonomous operation through the simplification of the mechanical design. The power generation subsystem will include a two-loop system paired with the heat pipes to allow for separation of fission products, increasing safety. Based on this separation of fission products, the subsystem will implement an open loop, in which atmospheric air is used as the coolant. The team selected the plate heat exchanger with a counterflow configuration based on efficiency and compactness. The heat exchanger will essentially act as a sleeve over the heat pipes. Shielding for the reactor is done in two parts. First, the core is surrounded by a 23cm lead shield. This shield is designed to protect workers from decay radiation when the reactor is off for transport and will allow for safe access to the reactor 12 hours after shutdown. The second shield is an operating shield made of dirt. The reactor will be placed into a pit, with soil built up around it. Additionally, a shipping container filled with shielding material will be placed on top of the reactor, to protect against air scattering of neutrons. From this shield design, a safe exclusion distance can be calculated. In operation, the exterior shield will have to be designed for the specific site that the reactor will be placed in depending on the industrial capacity and soil composition of the site.