This project explores the possibility of implementing a molten salt thermal energy storage system with a nuclear reactor in an existing grid. We started with the Advanced Fast Reactor 100 (AFR-100) design from Argonne National Labs as a reactor with which to pair our conceptual molten salt storage system. The AFR-100 was ideal based both on size and the use of supercritical carbon dioxide as a working fluid. The initial specified reactor concept allowed us to approach the different subsystems and decisions from a defined baseline. We began by developing a rough design and equations for a molten salt thermal storage system that could theoretically be attached to our sample reactor. The design focused on a number of smaller decisions such as the heat exchanger, type and volume of salt, etc. Then we looked at the ways that design could change to accommodate other reactor types and additional systems. Finally we considered the economic implications and cost efficiency of adding a molten salt thermal storage system to a nuclear reactor.
Team: Runa Archer, Charles Chapski, Jesse Hannan, Alexandra Laing, Claire Schmittinger
Project Advisor: Dr. Shanbin Shi, Dr. Bimal Malaviya
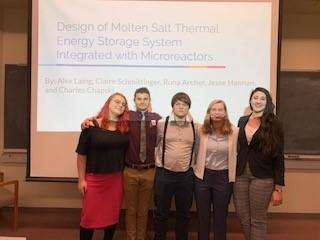
Members of the design group
Project Motivation
The main issue nuclear power faces in a decarbonizing energy grid is the challenge of dispatchability. Dispatchable energy, or energy which can increase or limit generation based on demand is an indispensable part of maintaining a power grid that operates safely while supplying enough energy to meet consumers’ needs, something carbon heavy sources are very capable of. Solar and wind output is limited by supply, and without modifications any light or wind is immediately converted to electricity. Nuclear has a similar problem except it is limited by its relative inability to start and stop quickly, rather than by supply. The advent of micro and small modular reactor systems, both featuring smaller reactors that can be operated independently of each other, are a partial answer to the dispatchability challenge. However, they are still limited to producing only at fixed quantities, for example, a 12 unit system of 10MW reactors could produce in increments of 10MW up to 120MW at full capacity. Large scale solar, another non-dispatchable carbon free energy source, has implemented molten salt thermal energy storage allowing it to vary its supply based solely on demand rather than just solar input. Adding thermal energy storage to a nuclear reactor system may make the improvements from smaller reactor concepts even more drastic, thus broadening nuclear’s place in a zero carbon future.
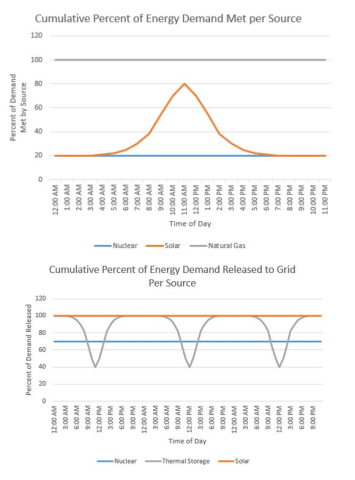
Figure 1
Project Description
This project explores the possibility of implementing a molten salt thermal energy storage system with a nuclear reactor in an existing grid. We started with the Advanced Fast Reactor 100 (AFR-100) design from Argonne National Labs as a reactor with which to pair our conceptual molten salt storage system. The AFR-100 was ideal based both on size and the use of supercritical carbon dioxide as a working fluid. The initial specified reactor concept allowed us to approach the different subsystems and decisions from a defined baseline. We began by developing a rough design and equations for a molten salt thermal storage system that could theoretically be attached to our sample reactor. The design focused on a number of smaller decisions such as the heat exchanger, type and volume of salt, etc. Then we looked at the ways that design could change to accommodate other reactor types and additional systems. Finally we considered the economic implications and cost efficiency of adding a molten salt thermal storage system to a nuclear reactor.

Figure 2
Results and Accomplishments
Several factors were identified in the design process that we decided to focus our designs on: (1) General design of the system; (2) The heat exchanger/reactor coupling systems; (3) The salt type and properties; (4) The pipes and tanks in the system; (5) The economic and environmental impacts. For the large scale design concept we chose to design a two tank molten salt system. The two tank system would allow for charging and discharging at the same time, as opposed to a one tank system which would only allow energy transfer in or out of the salt at a given time. The two tank system would also allow for more ease of maintenance on one tank should the system need to be shut down and a more complete energy transfer than a one tank system with a gradient, allowing for faster start up and shut down. The heat exchanger design chosen was the twisted tube heat exchanger. This design is very similar to the traditional shell-and-tube type heat exchanger, except that the tubes are twisted to maximize the heat transfer surface area. It also does not have baffles like the traditional shell and tube, which allows for a uniform flow distribution and velocity. In order for the system to be coupled with other reactors, the size of the heat exchanger can be varied based on the thermal output of the reactor- a smaller reactor having a smaller heat exchanger and vice-versa. Using HITEC as the thermal salt allows for optimal thermal properties and a smaller volume at the identified operating temperature of 500℃, as well as a very slow rate of degradation when compared to more affordable salts. This means a greater potential for scaling as well as minimal salt loss over a 30 year refueling period. The pipe and tank system analysis is very straightforward, and various equations that characterize the fluid behaviors and pressure losses were identified so that the necessary fluid pumping power for the system can be calculated. These equations can be used to determine an optimal pipe and tank design based on the specifications of the reactor to be coupled with. Ultimately, it was determined that this system would be viable for coupling with a small modular reactor/microreactor system. This would be extremely beneficial because, ideally, it would allow for the reactor to be operating at 100% capacity all the time, while releasing power only when needed. The ability to modify output is extremely economically beneficial because it allows for maximum production as well as maximum possible profits from the energy produced. It is also very beneficial from an environmental standpoint because nuclear power is a carbon-free energy source, which in some areas in the US already has an economic benefit and will likely allow companies who make use of this technology to be ahead of the curve as more serious environmental standards are developed and enforced.