There were several goals for the project. First, a literature survey of BWR containment designs and safety characteristics was performed. One of these designs, the Mark I is pictured in figure 1. Next, station blackout accidents were analyzed in several capacities. One capacity was the scenario, progressions, outcomes of such an accident. The other capacity of station blackouts that was analyzed was the potential consequences and societal impacts. These societal impacts were analyzed in depth in the case of Fukushima in the problem statement report which was completed early in the semester. Finally, passive safety-enhancing systems based on those thermodynamic analyses will be proposed.
Team: Alexander Depillis, Nicholas Ruzicka, Julianna VenDouern, Christian Wenger, John
Project Advisor: Dr. Michael Podowski
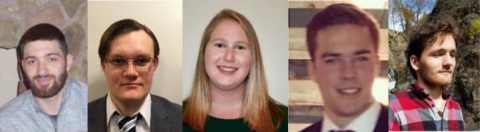
Members of the design group
Project Motivation
The accidents at Fukushima Daiichi were caused not by the earthquake, but by the ensuing tsunami, which severed the plant’s connection to the power grid and knocked out the backup diesel generators, leaving the reactors without power. The reactors had each a successful scram at the onset of the tsunami, meaning that the control rods were fully inserted. However, In the simplest possible terms, the accidents at Fukushima Daiichi were caused by the inability to remove decay heat from the reactor core. The decay heat generated by the core increased the pressure in the then stagnant primary loop. When the pressure in the primary loop met design limits, steam was automatically released from the reactor pressure vessel (RPV) into the drywell of the containment building by means of a safety relief valve (SRV). As the pressure in the drywell increases from superheated steam released from the RPV, the air-steam mixture in the drywell will be forced through downcomer pipes leading to the wetwell. In a Mark I containment building, the wetwell is a torus shape approximately half full of water. The wetwell and drywell are not designed to contain the high pressure that builds up from the injection of steam from the RPV for long periods of time and eventually will rupture explosively releasing radioactive steam and possibly damaging the RPV.
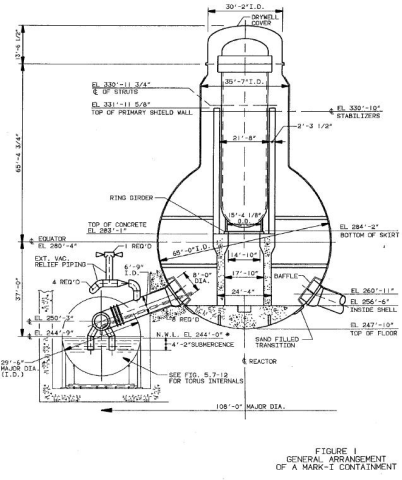
Figure 1
Project Description
There were several goals for the project. First, a literature survey of BWR containment designs and safety characteristics was performed. One of these designs, the Mark I is pictured in figure 1. Next, station blackout accidents were analyzed in several capacities. One capacity was the scenario, progressions, outcomes of such an accident. The other capacity of station blackouts that was analyzed was the potential consequences and societal impacts. These societal impacts were analyzed in depth in the case of Fukushima in the problem statement report which was completed early in the semester. Finally, passive safety-enhancing systems based on those thermodynamic analyses will be proposed.
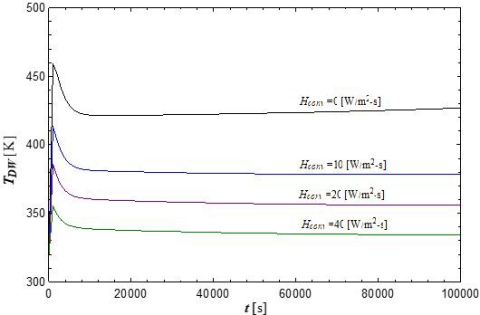
Figure 2
Results and Accomplishments
This semester we were able to complete the tasks set forth by the project. The literature review gave us an overview of the current safety systems and ideas for possible improvements to the Mark I containment design. We were able to work on a mathematical model to simulate heating during the accident conditions. This model gave us information on how much the containment would heat up and the amount of time it would take for it to fail. This mathematical model then allowed us to investigate improvements to the Mark I containment design. The results for the temperature change in the drywell over time (one of the parameters of the model) is shown in figure 2. Our suggestion for mitigation would be to add a heat exchanger to the containment which could be connected to the wetwell to dissipate some of the heat that is already transferred there. The heat exchanger we are most looking at is a printed circuit heat exchanger. These heat exchangers are created without joints, seams, or gaskets which allows for a singular piece unit that reduces the places in which the system can fail. Because of the construction of these single piece units they can be crafted with the largest range of operating parameters to be suited for the many different BWR’s in the market. This way the heat exchangers could not only be adapted to new units, but also integrated into older currently operating reactors. These heat exchangers have a reduced flow rate which helps save on operation cost, and a smaller compact unit which saves on materials and construction along with the smaller size making it easier to adapt to older reactors.