The design of the bore needed to contain a diameter of at least 70.1 inches in order to fit the MPC as well as a depth of 50 meters to allow for the storage of 10 MPC in each bore. The diameter and depth of the drilling is dependent on already existing technologies because it would not be cost effective to develop new technology for this project. In our borehole storage design, canisters will be stacked on top of one another. The combined loading due to stacking canisters results in substantial axial stresses. Structural analysis of the bottom canister, the limiting component, was performed to verify that it will not fail under normal loading conditions. Using the thermal modelling software Tough2, the temperature profiles for multiple rock and soil moisture contents were created. These profile were constructed using the maximum decay heat generation rates for the used fuel within the MPC, and the limiting centerline temperatures were calculated less than the limit. The MPC surface and near dose radiation was simulated using MCNP to determine if the canister meets the current NRC guidelines. Both neutron and photon analysis was performed using data that represented a 10 year cooling time period after initial spent fuel pool storage.
Team: Erin Amarello, Richard Bennett, Jeff Keegan, Jarrod Prescott
Project Advisor: Dr. Wei Zhou
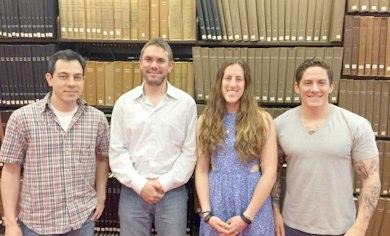
Project Motivation
The goal of the Improved Extended Storage of High Burn-Up Used Nuclear Fuel (UNF) project is to create a better way to store the used nuclear fuel from the 61 nuclear power plants here in the United States. The benefits of this approach have significant improvements over the current system of storage. In addition to space savings on existing storage sites with the underground storage concept, there would be an increased amount security around the canister. In addition to this concept, limiting the exposure to the atmosphere, the susceptibility of corrosion is reduced. Cost is an additional aspect when building any containment that will last over 100 years. These factors together show incentive for creating a new design in dry waste storage.
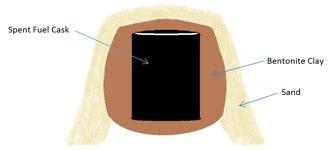
Project Description
The design of the bore needed to contain a diameter of at least 70.1 inches in order to fit the MPC as well as a depth of 50 meters to allow for the storage of 10 MPC in each bore. The diameter and depth of the drilling is dependent on already existing technologies because it would not be cost effective to develop new technology for this project. In our borehole storage design, canisters will be stacked on top of one another. The combined loading due to stacking canisters results in substantial axial stresses. Structural analysis of the bottom canister, the limiting component, was performed to verify that it will not fail under normal loading conditions. Using the thermal modelling software Tough2, the temperature profiles for multiple rock and soil moisture contents were created. These profile were constructed using the maximum decay heat generation rates for the used fuel within the MPC, and the limiting centerline temperatures were calculated less than the limit. The MPC surface and near dose radiation was simulated using MCNP to determine if the canister meets the current NRC guidelines. Both neutron and photon analysis was performed using data that represented a 10 year cooling time period after initial spent fuel pool storage.
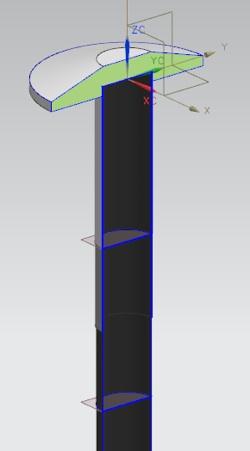
Results and Accomplishments
The analysis concludes that the bore design is a feasible way to meet the increased storage need of the nuclear industry. Research has shown that technology to create the proposed bore hole design exists and is currently being used by International Association of Foundation Drilling. The design consists of a bore created with a hydraulic drill rig that is 50 meters deep and nearly 2 meters in diameter. The bore will have a seal consisting of 0.5 inches of cement lined with 0.5 inches of stainless steel with a 0.5 inch air gap between the seal and the MPC. Stress Analysis concluded that the MPCs can withstand all the stresses associated with the stacking incorporated in this storage design. The thermal analysis shows that the temperature of the centerline can be kept below the 400 C technical specification with results concluding that the maximum centerline temperature would be 331.22 C and that it would only take 35 meters of distance from the centerline of the MPC for the ground to reach ambient temperature. The radiological analysis using MCNP shows that the technical limitation for the contact surface dose rate of 200 mrem/hr would not be violated.